水素社会の中核となる新鋼材開発
|
日本製鉄が開発した『HRX19』は耐水素脆性と強靱性、そして溶接を可能にした画期的な高強度ステンレス鋼だ。来る水素社会インフラの中核である水素ステーションや、高圧水素を搭載する燃料電池車への活用が広がっている。従来、水素ステーションに使用できる鋼材はステンレス鋼『SUS316L』だけだったが、強度が低く、水素圧向上に対応するには配管を肉厚にし、機械継手で接続していた。その結果、敷地や設備が大きくなり、建設費が増加。加えて機械継手には水素漏れの懸念があるため、常に保守費用を見込まねばならず、ステーション普及の障害になっていた。新たな高強度ステンレス鋼の研究スタートは、2003年にさかのぼる。将来的な水素エネルギーの需要を見越し、NEDO(新エネルギー・産業技術総合開発機構)とも協力しながら、まずは高圧水素用評価技術の確立を目指した。06年、既存材料の性能を把握し、高圧水素環境下に耐えうる材料メカニズムの基盤を構築。08年、高強度かつ溶接可能な材料分野にフォーカスした成分検討が開始される。そして2010年には、『HRX19』の開発が完了。その後、14年から15年にかけ、材質と溶接の認可を相次いで受け、時を同じくして初受注も達成した。
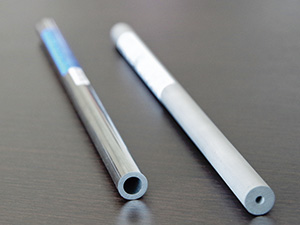 「HRX19」鋼管(左)と 「SUS 316L」鋼管(右)の比較 |
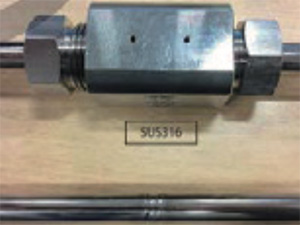 「SUS316L」機械継手(上)と 「HRX19」溶接継手(下)の比較 |
|
高圧水素のニーズに迅速に応えた開発体制
|
『HRX19』が画期的な鋼材となった技術ポイントは、大きく二つある。ひとつは、耐水素脆性と高強度の両立だ。水素分子は極小なので金属に侵入しやすく、金属結合を弱める「水素脆化」が起きる。そのため、鉄の厚肉化を避けながら、強度と耐水素脆性を達成するのは至難だ。水素圧が低ければ、既存材料でも対応方法はある。しかし、車の航続距離を伸ばすためには、車載の水素量やステーションの水素圧の上昇は必須。研究開始時点で、将来の燃料電池車および水素インフラ基地の整備を担う鋼材開発を目指していたため、それが実現できる高強度、かつ高い耐水素脆性が求められた。事実、2008年頃には、燃料電池車の周辺用途として、これまで30MPa前後だった水素圧を70〜85MPaにする要望が聞かれ始めた。これほど高圧のニーズは、他の製品やLNGなどのガスでは前例がない。開発陣は未だかつてない挑戦に対し、高強度化手法として窒素を含んだ「固溶強化」に着目。鉄結晶の転位構造と水素脆化のメカニズムを解き明かした。調べた結果、耐水素脆性がある従来の『SUS316L』では転位構造がセル化しているが、高窒素なステンレス鋼ではプラナー化しており、脆化原因となる知見を得た。そこで、転位構造をセル化するCr(クロム)やMn(マンガン)などを増量し、高圧水素に耐えつつも目標強度800MPaを両立させた。開発チームが短期間で要求性能に応えられたのは、かねてより水素環境下の材料評価や機構解明を精査していたことが大きく寄与した。
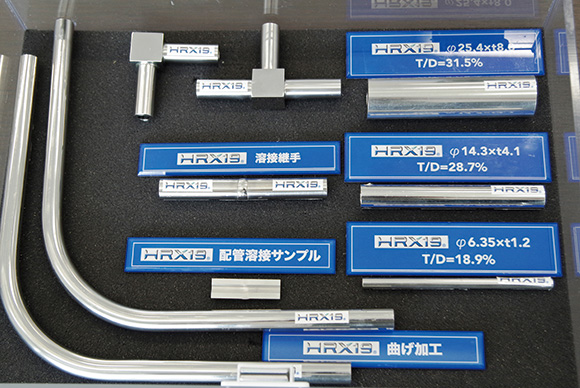 『HRX19』鋼管の加工バリエーションのサンプル。とてもコンパクトに加工できる。
|
|
耐水素脆化性と強度化に溶接性を付加
|
二つ目に挙げられるのは、新ステレンス鋼の溶接施工が可能であることだ。しかし、当初は難しい問題があった。『HRX19』は多くの窒素を溶かし込んで耐水素脆性を上げるが、溶接する際に窒素が抜け出し、強度低下および水素脆化を招くフェライト相の生成が確認された。この解決策として、アーク溶接時のシールドガスに適量の窒素を添加し、溶接の入熱を調整して、窒素離脱を抑制。その最適条件を見出すことで、溶接部分も本管と同じ高強度と耐水素脆性を両立できる、鋼管の自動溶接を可能にした。そして『HRX19』では、ユーザごとに異なる溶接条件にも対応するため、基本となるデータベースを構築し、溶接部の品質を確保。鉄を知り尽くすプロならではの細やかな気づかいが、新材料への不安を払拭して製品化を後押しした。
|