リチウムイオン電池に安全性を付与する
|
リチウムイオン電池は小型かつ軽量の蓄電池として、現在ではPC、スマートフォンなどの携帯電子機器の電源に広く利用されている。その原理は単純化すると、「正極と負極を隔てる液体電解質の中を、リチウムイオンが往来し、放電・充電を行う」ものだ。しかし、電解質に可燃性の有機溶媒が使用され、発熱・発火など安全性には細心の注意を要する電池系でもある。特に電気自動車の車載や電力貯蔵用への利用にともない大型化すれば、電解質量の増大と放熱性の悪化を招き、安全性の問題は極めて深刻だ。そのため、電解質に不燃性の固体電解質を用いる「電池の全固体化」は、リチウムイオン電池に高水準の安全性を付与する技術として期待が高まった。高田さんが全固体電池に関わり始めたのは、1986年に松下電器産業(現・パナソニック)へ入社した時から。1991年に国内他社からリチウムイオン二次電池が発売され、いよいよ電解質に有機溶媒を使用しないリチウム系の研究が本格化した。
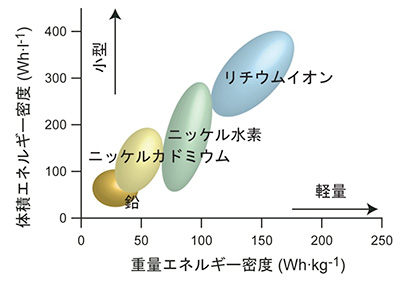 電池の変遷
リチウムイオン電池は小型軽量かつ、高いエネルギー密度を誇る。
|
|
全固体電池に立ちはだかる出力の課題
|
全固体電池の実用化へ向けてまず取り組んだのは、液体電解質並みのイオン伝導性を示す固体電解質である。当時、このような要求性能を満たす素材はヨウ化リチウムを添加した硫化物ガラスだったが、電気化学的な安定性が低く、リチウムイオン電池の正極側のLiCoO2(コバルト酸リチウム)に対する適合性が良くなかった。そこで高田さんの研究チームは、新たな固体電解質の開発に着手し、高いイオン伝導性と耐酸化性を兼ね備えた特殊ガラスを開発。一方、黒鉛を使う負極側でも電解質の骨格構造と耐還元性の解明・研究が進み、正・負極に異なった固体電解質を使用するという独自の電池構成が完成した。これは固体化ゆえの利点であり、これらの組み合わせは、高いエネルギー密度の達成に大きく寄与した。最終的には正・負極側に対する耐酸化性と耐還元性をあわせもつ固体電解質が開発されたが、新たな全固体電池においてもまだ出力特性の低さが課題だった。イオンは一般的に液体中のほうが動きやすいため、固体電解質の電池では高出力は望めないことが通念だった。そのため、高いイオン伝導性を持つ素材は必須で、それまでも試行錯誤の末に何種類もの固体電解質が開発されてきた。だが、この時点でも全固体電池の出力電流は、従来型リチウムイオン電池の数分の1程度にとどまり、多くの研究者はさらなるイオン伝導性の向上を目指していた。
|
界面抵抗への着目が、実用化へのブレークスルーに
|
当初は高田さんのチームも同様の研究を行っていたが、方向性に疑問を感じ始める。“正極から大きな電流を取り出せない事象”は、どうすれば説明できるのか。高田さんは、「酸化力の高い正極が接触すると、硫化物電解質の接触した部分でリチウムがほぼなくなると考えた」と、当時のひらめきを語る。この仮説を元に、電池の出力を左右する律速段階を調べ、原因が固体電解質内のイオン輸送過程ではなく、正極活物質と固体電解質との“界面抵抗”に端を発することを突き止めた。硫化物の固体電解質は本来高いイオン伝導性を持つが、正極との接触面でリチウムイオン欠乏層が形成され、ここで伝導性が大きく下がることを確認。イオン伝導体が接触する界面で起こす特異な挙動は「ナノイオニクス」と呼ばれ、現象自体は90年代から知られていたが、全固体電池の界面でのクリティカルな現象となっていたのだ。高抵抗の要因が判明し、対処法が明確化した。正極の界面をリチウムイオン伝導性を持つ酸化物で被覆(薄膜の緩衝層形成)したところ、界面抵抗の低減に成功。全固体リチウムイオン電池の出力性能は、現行リチウムイオン電池に匹敵するまでに向上。現在の出力はそれをも上回るものになっている。さらに、共同研究先企業の要望に応じ、被覆工程を省略し、固体電解質にアルミ化合物を添加する方式で、高出力と低コスト化を可能にもした。
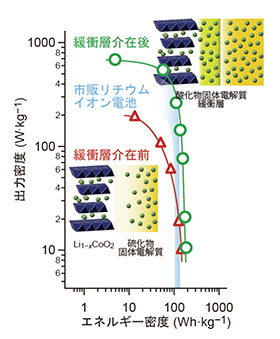 緩衝層による界面抵抗の低減と出力向上
固体電解質が正極に接触した界面では、リチウムイオン濃度が低下した空間電荷層が形成される。この層は非常に高抵抗で、出力性能を低下させる。そこで、界面に酸化物固体電解質の薄膜を設け、イオン欠乏への緩衝層とし、出力を回復・向上させた。
|
|